7 Pallet Rack Safety Tips for Warehouse Managers Who Want Fewer Accidents
by Brian Reaves, on Sep 16, 2022 7:00:00 AM
Warehouses can be dangerous places to work. The U.S. Bureau of Labor Statistics reports that 4.8 out of every 100 warehouse workers will be injured on the job. In addition, the National Safety Council states that falls from height are the third most common cause of workplace injury. And collapsing pallet racks are a significant contributor to the fourth most common cause, contact with objects and equipment.
Failing to follow warehouse pallet rack safety guidelines is the leading factor in these accidents. Thankfully, you can take steps to protect your team's safety. Read on to learn 7 ways to improve pallet rack safety.
1. Start Off Right
Faulty pallet rack installation is one of the most common reasons for OSHA citations. DIY installation is a significant cause of racking collapse. This is because installation errors dramatically limit the unit's load capacity.
Professional pallet rack installation is the best way to ensure correct installation. A professional installation guarantees your units meet OSHA standards. This means freestanding racks are limited to 8 feet, with taller racks adequately anchored.
Finally, professional installation can also include rack protection devices. Forklift collisions cause 90% of pallet rack failures. Guards and railings installed around uprights are a simple but effective way to prevent this damage.
2. Load With Pallet Rack Safety In Mind
OSHA pallet rack requirements demand that all racks be labeled with the beam load capacity. This value appears in pounds per level. And it must be listed on every tier above ground level.
This is particularly important as a pallet’s weight limit might exceed the rack’s. Without knowing the rack's load capacity, workers cannot know if a pallet must be repacked before storing.
Additionally, the lowest pallet levels hold the heaviest loads. A storage pattern of heavy on the bottom and light on top adds stability to racks. This increases pallet rack safety which improves warehouse safety overall.
3. Make Daily Inspections Your Goal
Make storage inspections a regular occurrence. Trained staff should conduct thorough pallet rack inspections at least once a month. However, a weekly inspection is encouraged, and daily visual evaluations are best to catch damage early.
These inspections should pay special attention to dings, dents, and rust. Even a small dent in the unit could be dangerous as it reduces the maximum load capacity. Likewise, rust decreases the strength of uprights and support beams. So, address found rust immediately.
Don’t ignore the condition of your pallets themselves. Broken, cracked, or splintered pallets are dangerous as they further reduce the posted beam load capacity. Replace damaged pallets right away.
At least once a year, a third-party inspector should do an in-depth inspection of all pallet racks. This inspection is essential to confirm the safety of units. Unload and repair any units that fail inspection to avoid costly OSHA penalties.
4. Invest in Expert Repair
Accidents happen despite the best intentions. So when damage occurs, have a plan to address it quickly. If damage can’t be repaired, unload the unit and tag it as out of service until appropriate repairs can be made.
Do not try to make homemade repairs. Improper repairs make pallet racks less safe. Inexpert field welding damages structural integrity, and reconfiguration affects the load capacity. Thus, all repairs must be certified by a qualified engineer. The bottom line is the risks of homemade repairs outweigh the rewards. Hiring expert service is much better than gambling with pallet rack safety.
5. Approved Modifications for the Win
As warehouse needs change, so do racking needs. However, a qualified engineer must oversee all changes to existing pallet racking. Remember, even small changes, like changing the height of a tier, can affect the whole unit’s load capacity. Don’t compromise pallet rack safety by making unapproved modifications to any warehouse storage.
When making changes, know that parts are not necessarily interchangeable. There are a ton of manufacturers who make pallet racks. And each uses its own design. Using parts from one company to fill in gaps on racking from another can be disastrous. There is no guarantee that parts from different manufacturers will perform as intended when used together. This incompatibility can cause severe hazards like load capacity reduction. Or even deadly conditions like beams could even dislodge during unloading.
6. Give Yourself Some Breathing Room
Space is money in any warehouse. So understandably, you want to maximize your storage capacity. But leave enough space for equipment such as forklifts and order pickers to maneuver.
Inadequate aisle space will increase the number of collisions between your equipment and your racks. This leads to an increase in pallet rack damage and a decrease in warehouse safety. So don’t let the temptation of a few extra feet of space cost you thousands in OSHA penalties or millions in lawsuits.
7. Create a Culture of Training
All the safety equipment in the world is useless if workers don’t know how to use it. Therefore, training warehouse staff is vital to ensuring they have the knowledge and skills to avoid accidents and deal with hazardous situations.
Ensure your staff is up to the challenge by providing them with annual safety training. Annual training ensures that safety standards do not drop off over the years.
During staff training, educate your team on the equipment used to protect them. This should include using stools or knee pads for work below waist level. It should also have reminders to use ladders of an appropriate height. OSHA pallet rack requirements dictate the top step of all ladders should be higher than the top level of the unit accessed.
There are a variety of organizations that provide online training on OSHA standards. This makes it easy to provide thorough training on current OSHA guidelines.
Find Your Ideal Storage Solution
Every warehouse is different. And you need a storage solution customized to your business. Luckily, SST can help. To learn more about storage rack safety guidelines and what storage solutions are right for you, contact our Solutions Team online or visit one of our locations throughout Florida and Georgia.
Florida
Jacksonville
Lakeland
Ocala
Orlando
Tampa
Winter Have
Georgia
Albany
Macon
Columbus
Valdosta
Further Reading
How Can I Protect My Pallet Racking?
Is It Better To Repair Or Replace Pallet Racking?
Is It Okay To Mix Racking Materials From Different Manufacturers?
Low-Level Access Lifts vs. Ladders
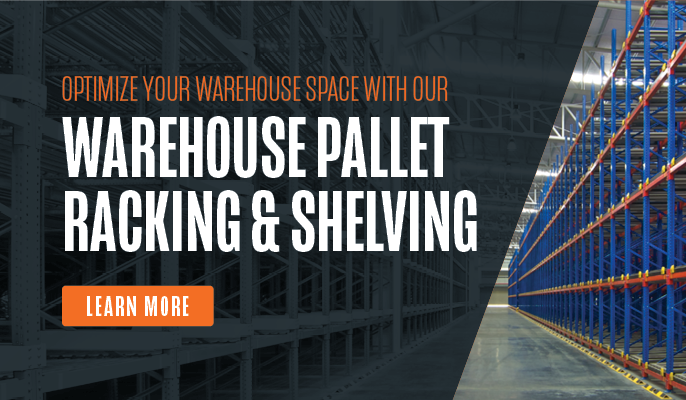